塑料片材挤出机的生产流程通常包括以下几个主要步骤:
原料准备:首先,根据所需生产的塑料片材的规格和性能要求,选择合适的塑料原料,如PP、PE、PS、PET、EVA、ABS等。原料通常以颗粒状或粉状形式存在。
原料干燥:为了确保产品质量,一些塑料原料(如PET、PC等)需要在使用前进行干燥处理,以去除水分和其他挥发物。
喂料:将干燥后的原料通过料斗送入挤出机的进料段。料斗通常配有防堵料和定量喂料装置。
熔融:原料在挤出机的机筒内被加热至熔融状态。机筒通常分为几个加热区,每个区的温度可以立控制,以适应不同的熔融和塑化要求。
塑化:熔融的塑料在螺杆的旋转作用下,通过剪切和搅拌作用进一步塑化,形成均匀的熔体。
过滤:塑化后的熔体在进入模具前通常要通过过滤网来去除杂质和未熔化的颗粒。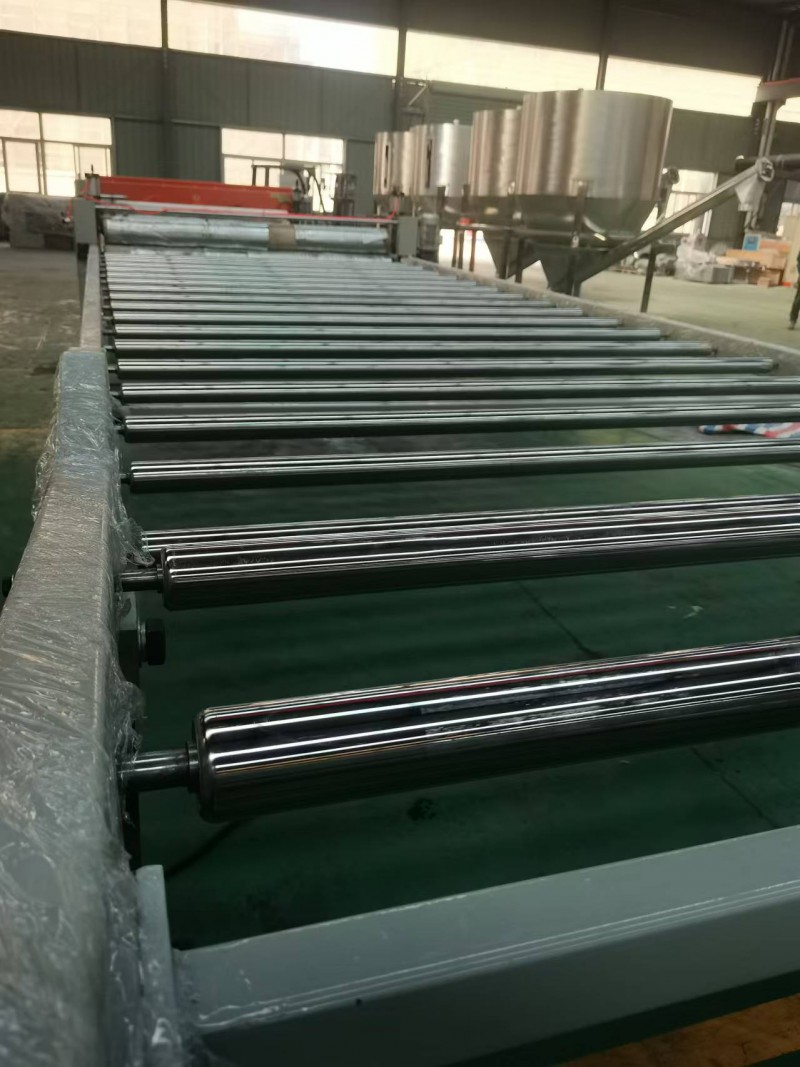
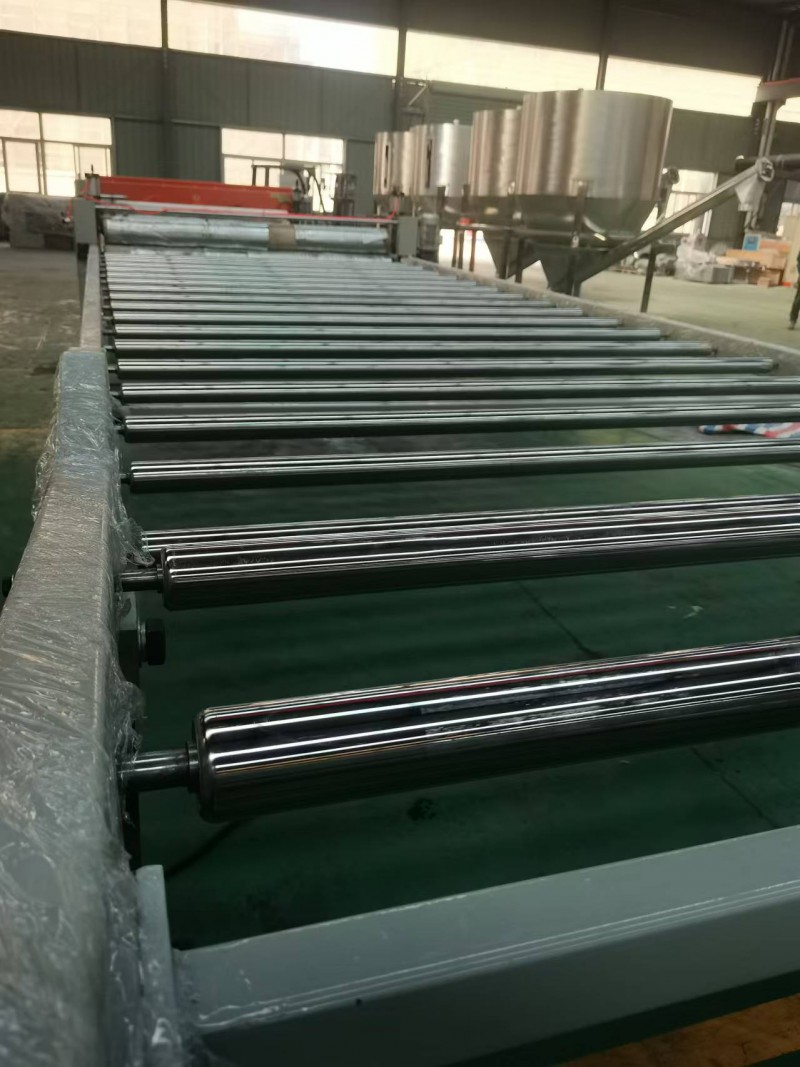
成型:熔体通过挤出机的模具,在模具的成型段形成所需的片材形状和厚度。
冷却:刚成型的塑料片材通过冷却装置(如冷却辊、冷却水槽等)进行冷却,以固化成型。
牵引:冷却后的片材通过牵引装置进行稳定牵引,保持一定的速度和张力。
切割:根据需要,将连续生产的片材切割成一定的长度或宽度。
卷取:后,将切割后的片材卷绕在卷取装置上,以便于储存和运输。
检验:在整个生产过程中,需要对片材的质量进行监控和检验,包括厚度、宽度、表面质量、物理性能等。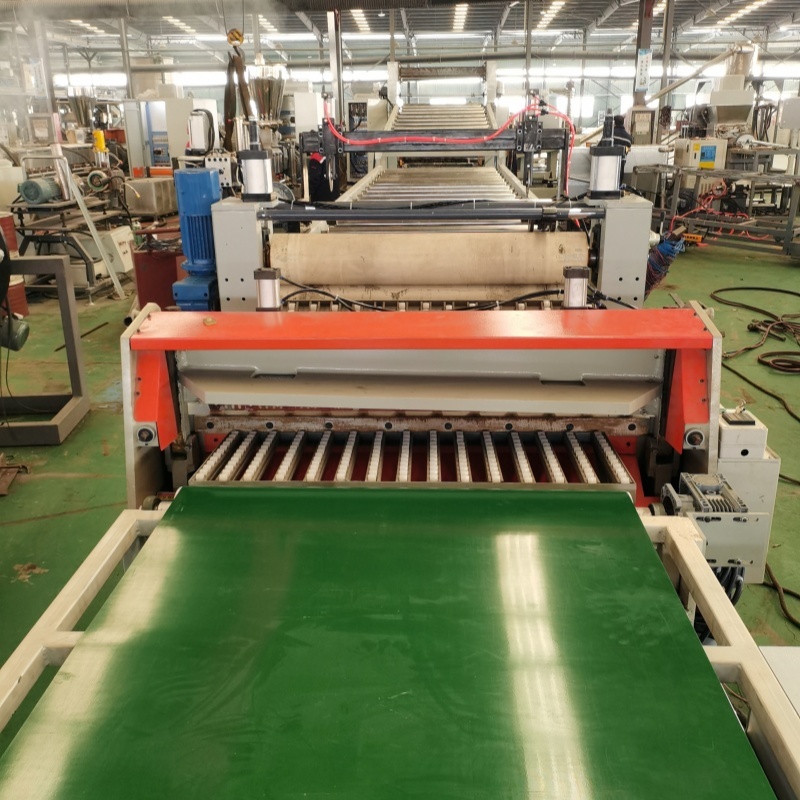
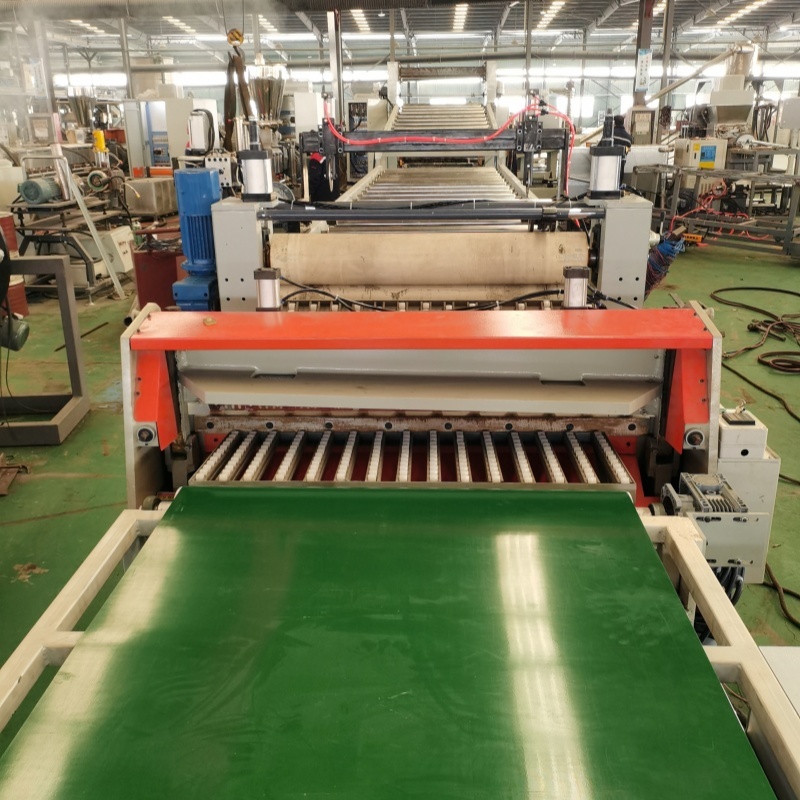
整个生产流程需要精确的控制系统来确保产品质量和效率。此外,为了适应不同的生产需求,挤出机的配置和参数可能需要调整。